Heute berichten wir über eine Simulationsstudie zur OEE-Optimierung an einer verketteten Produktionsanlage. Auf dieser Anlage wird eine Vielzahl an unterschiedlichen Baugruppen vollautomatisch montiert.
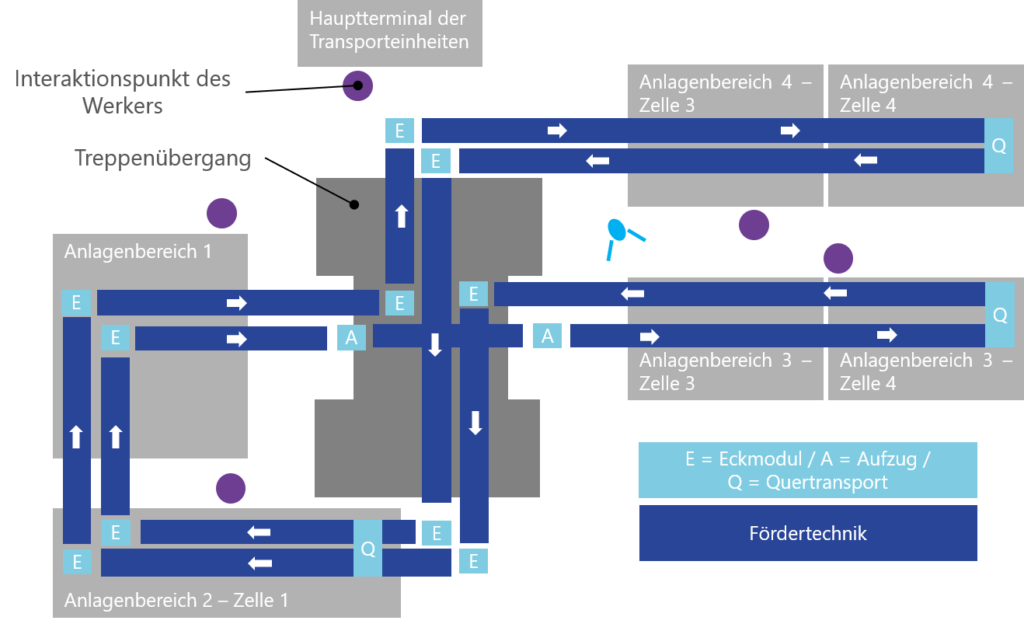
Um den Overall-Equipment-Effectiveness (OEE) der Anlage zu steigern, etablierte das Lean-Team bereits erfolgreich KVP und nutzte die Wertstromanalyse. [1] Diese führten allerdings nicht zu dem angestrebten OEE-Zielwert. Da die Vielzahl an verketteten Prozessen (mehr als 20 Montagestationen mit verkettetem Materialfluss) mit hohen Wechselwirkungen und den dynamischen Einflüssen nicht ausreichend erfasst werden konnten. Dies behinderte die Aussage über Auswirkungen von technischen Veränderungen. [2]
Damit das Lean-Team zielgerichtete Entscheidungen treffen kann, wurde eine Simulationsstudie in Auftrag gegeben. Das Ziel war die Erstellung eines digitalen Modells der Produktionsanlage, mit welchem „Was-Wäre-Wenn-Szenarien“ durchgeführt und mögliche Optimierungspotentiale abgesichert werden sollten.
Eine Simulationsstudie ist gemäß VDI 3633 ein „Projekt zur simulations-gestützten Untersuchung eines Systems“ und lässt sich in die Phasen: Aufgabendefinition, Systemanalyse, Modellformalisierung, Implementierung, Datenbeschaffung und -aufbereitung, Experimente und Analyse, sowie Verifikation und Validierung (V&V) untergliedern. [3]
Mehr zum Inhalt der einzelnen Phasen einer Simulationsstudie erhalten sie hier.
Während der Systemanalyse wurde eine Beschreibung der abzubildenden Produktionslinie angefertigt. Diese wurde in der Modellformalisierung weiter spezifiziert, um das Simulationsmodell erstellen zu können. Dieses konnte mit bestehenden Daten eines installierten MDE/MES-Systems validiert werden, sodass Gewissheit bestand, dass das Simulationsmodell die Realität hinreichend genau abbildet. Daten über technische Störungen oder Eingriffe durch den Bediener wurden durch Multimomentaufnahmen erfasst und ebenso im Simulationsmodell berücksichtigt.
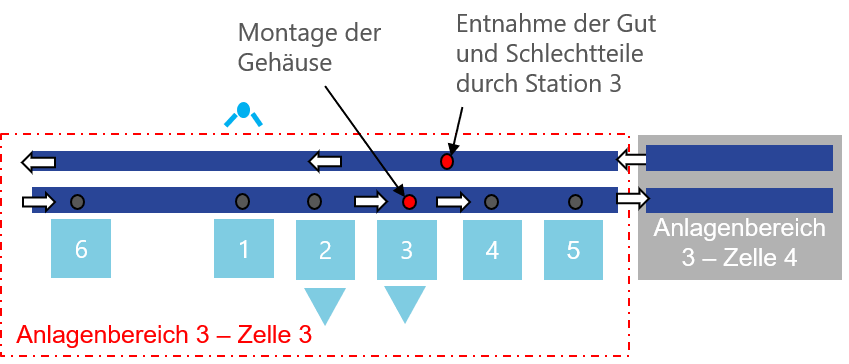
Durch die Simulationsstudie wurde ein digitales Abbild der bestehenden Produktionsanlage geschaffen, bei der dynamische Einflüsse der Anlage, der produktspezifisch zu verarbeitenden Materialien und die Einflüsse des Anlagenbedieners berücksichtigt wurden. Dies ermöglicht eine Überprüfung möglicher Optimierungspotentiale (Was-Wäre-Wenn-Szenarien). Hierzu wurden Parameter variiert (z. B. Prozess-, Störzeiten, Fördergeschwindigkeiten, Puffergrößen, Anzahl Werkstückträger, Mitarbeiteranzahl), sowie Konfigurationen verändert und simuliert. Am Durchsatz pro Schicht ließen sich die Anpassungen bewerten und zeigten z. T. erhebliche OEE-Potenzial auf. Die Simulation ermöglichte die Bestimmung der sinnvollsten Verbesserungen als auch die effektivste Umsetzungsreihenfolge. Durch eine technische Bewertung inkl. Kostenermittlung sind die Grundlagen für eine abgesicherte ROI-Entscheidung (Return on Investment) geschaffen. Zukünftig wird das Simulationsmodell an Veränderungen, neue Produkte, Umbauten angepasst und so für weitere Optimierungen genutzt.
Wollen Sie Ihre Produktions- und Logistiksysteme digital abbilden und optimieren oder Ihre Ideen und Konzepte durch eine Simulation überprüfen und absichern, dann kontaktieren Sie uns gerne.
Quellen
[1] | Erlach, K.: Wertstromdesign – Der Weg zur schlanken Fabrik, 3. Auflage. VDI-Buch, Berlin Springer-Verlag GmbH, 2020 |
[2] | Winkler, H.; Lugert, A.: Die Wertstrommethode im Zeitalter von Industrie 4.0 – Studienreport. Cottbus, Brandenburgische Technische Universität Cottbus-Senftenberg, 2017 |
[3] | VDI Richtlinie 3633 Blatt 1: Simulation von Logistik-, Materialfluss- und Produktionssystemen – Grundlagen. Berlin, Beuth Verlag GmbH, 2014. |