Der Transport von Gütern umfasst ca. 72,3 % des gesamten Gütertransports in Deutschland. [1] Hierbei ist die manuelle Be- und Entladung durch Stapler mit erheblichen Lkw-Standzeiten, einem Staplerbetrieb und entsprechenden Kosten verbunden. Daher kommen seit Jahrzehnten immer häufiger automatische Be- und Entladesysteme für regelmäßige Transportstrecken zum Einsatz. [2]
Dies gilt insbesondere für kurze Transportstrecken, da hierbei der Zeitanteil für die Be- und Entladung, im Verhältnis zur Fahrzeit, groß ist und daher eine automatische Be-, Entladung ein erhebliches Einsparpotenzial bietet. [3] Somit sind automatische Be-, Entladesysteme im Werksverkehr sowie bei einem regelmäßigen Transport zwischen Produktionsbetrieben und Logistikzentren heute der Standard.
Die Installation der Be- und Entladeeinrichtungen im Produktionswerk und im Logistikzentrum als auch die Ausstattung der Lkw-Auflieger ist mit erheblichen Investitionen verbunden. [4] Daher ist bei der Planung die Anzahl der notwendigen Be-, Entladeeinrichtungen als auch die Anzahl der Lkw-Auflieger zu bestimmen. Eine statische Betrachtung mit durchschnittlichen Fahrzeiten und durchschnittlichen Be-, Entladezeiten ist jedoch nicht ausreichend. Es bedarf einer dynamischen Betrachtung über die Zeit, u. a. da:
- die Lkw-Fahrzeit je nach Streckenführung, Verkehrsbelastung (Hauptverkehrszeit, Verkehrstau, etc.) stark schwanken kann.
- die Lkw-Standzeit zur Beladung im Produktionsbetrieb schwanken kann, aufgrund von nicht ausreichend bereitstehenden Paletten für die Verladung.
- die Entladeeinrichtung des Lkws kann nicht angefahren werden kann, weil diese durch einen weiteren Lkw blockiert wird.
Besonders wirtschaftlich ist der Einsatz der automatischen Be- und Entladung, wenn dadurch im Produktions- und/oder im Logistikbetrieb der Staplerverkehr vermieden oder drastisch reduziert werden kann.
Angesichts dessen wird der Palettentransport im Produktionsbetrieb meist durch Fördertechnik so gestaltet, dass die Fertigware von der Produktionsanlage oder dem Palettiersystem automatisch zur Verladeeinrichtung transportiert wird. Hierbei stellt die Verladeeinrichtung und die Fördertechnik einen gewissen Palettenpuffer dar. Nachteilig ist jedoch, dass die Produktionsanlage bei Rückstau, z. B. weil kein Lkw zur Beladung verfügbar ist, zum Stillstand kommt. Dadurch entstehen in der Produktion erhebliche Stillstandskosten und ggf. Lieferterminprobleme. Dies gilt es zu vermeiden. Daher ist auch hier eine dynamische Betrachtung mithilfe einer Simulation notwendig, u. a. da:
- auf den Produktionsanlagen unterschiedliche Artikel (z. T. bis zu mehreren Hundert) hergestellt und verpackt werden und die Menge der Paletten pro Zeiteinheit, in Abhängigkeit des produzierten Artikels, stark schwanken kann.
- technische Störungen an den Produktionsanlagen, Rüst- und Reinigungszeiten, die Anzahl an Paletten je Zeiteinheit stark variieren lassen.
- im Produktionsbetrieb i. d. R. nicht jede Produktionsanlage mit einer eigenen Palettenverladung ausgestattet ist, führt der Palettentransport meist von mehreren Produktionsanlagen auf eine oder zwei Verladeeinrichtungen.
- jede artikelspezifische Palette ein unterschiedliches Gewicht hat und die maximal zulässige Zuladung des Lkws nicht überschritten werden darf. Dies führt in der Praxis dazu, dass ggf. ein Lkw 33 EPAL (Europaletten) laden kann, aber aufgrund der Gewichtsrestriktion nur 27 EPAL aufnehmen darf.
Somit entsteht eine hohe Varianz, die in einer Simulation dynamisch abgebildet werden muss.
Mit dieser Herausforderung beschäftigte sich ebenfalls einer unserer Kunden, einem Unternehmen aus der Getränkebranche. In Zusammenarbeit mit der AcuroSim soll dabei das Transportkonzept (inkl. automatischer Verladesysteme und Leergutbereitstellung) von der Produktionsstätte bis zum ca. 20 km entfernten Logistikzentrum untersucht werden. Dabei standen insbesondere folgende Fragen im Fokus:
- Welchen Einfluss haben unterschiedliche Routen/Wegführungen an den jeweiligen Wochentagen und zu den unterschiedlichen Uhrzeiten (24/7) auf die Transportkapazität?
- Welchen Einfluss haben die Lenk- und Pausen-Zeiten der Lkw-Fahrer? Lohnt sich ein Springereinsatz in der Pause?
- Welchen Einfluss haben unterschiedliche Produktionspläne und Artikel-Linien-Kombinationen auf den Transportbedarf?
Welches Konzept der automatischen Verladesysteme im Produktionsbereich und im Logistikzentrum sind am besten geeignet?

Vor der Implementierung des Simulationsmodells erfolgte zunächst eine Analyse des gesamten Systems. So wurden insbesondere die folgenden Fragen diskutiert:
- Wie gestaltet sich der Materialfluss von Fertigware, vom Produktionsbetrieb zum Logistikzentrum?
- Wie ist der Materialfluss des Leerguts, welches im Logistikzentrum angeliefert wird und dem Abfüllbetrieb zugeführt werden soll, geplant?
- In welchen Zeitintervallen steht die Fertigware für den Abtransport bereit? Wann muss entsprechendes Leergut für die Produktion bereitgestellt werden und welchen Einfluss hat das unsortierte Leergut (fehlerhafte und fehlende Flaschen in den Getränkegebinden) auf die Transportbedarfe?
- In welcher Reihenfolge sollen die Be- und Entladeeinrichtungen im Produktionswerk als auch im Logistikzentrum angefahren werden?
- Wie viele automatische Be- und Entladeanlagen werden im Produktionswerk benötigt? Wie viele im Logistikzentrum? Und wie viele Lkw Auflieger sind mit den entsprechenden Transporteinrichtungen auszustatten?
Neben der Ablaufbeschreibung des Systems müssen vielfältige Daten gesammelt, analysiert und aufbereitet werden. So konnte beispielsweise auf die Frage „In welchem Zeitintervall steht die Fertigware für den Abtransport bereit?“ auf erfasste Zeitstempel der NVE (Nummer der Versandeinheit) – Etikettendrucker zurückgegriffen werden. [5] Anhand dieser Daten wurde für jedes Produkt und Linie eine individuelle Ankunftsverteilung erstellt und später im Simulationsmodell integriert.
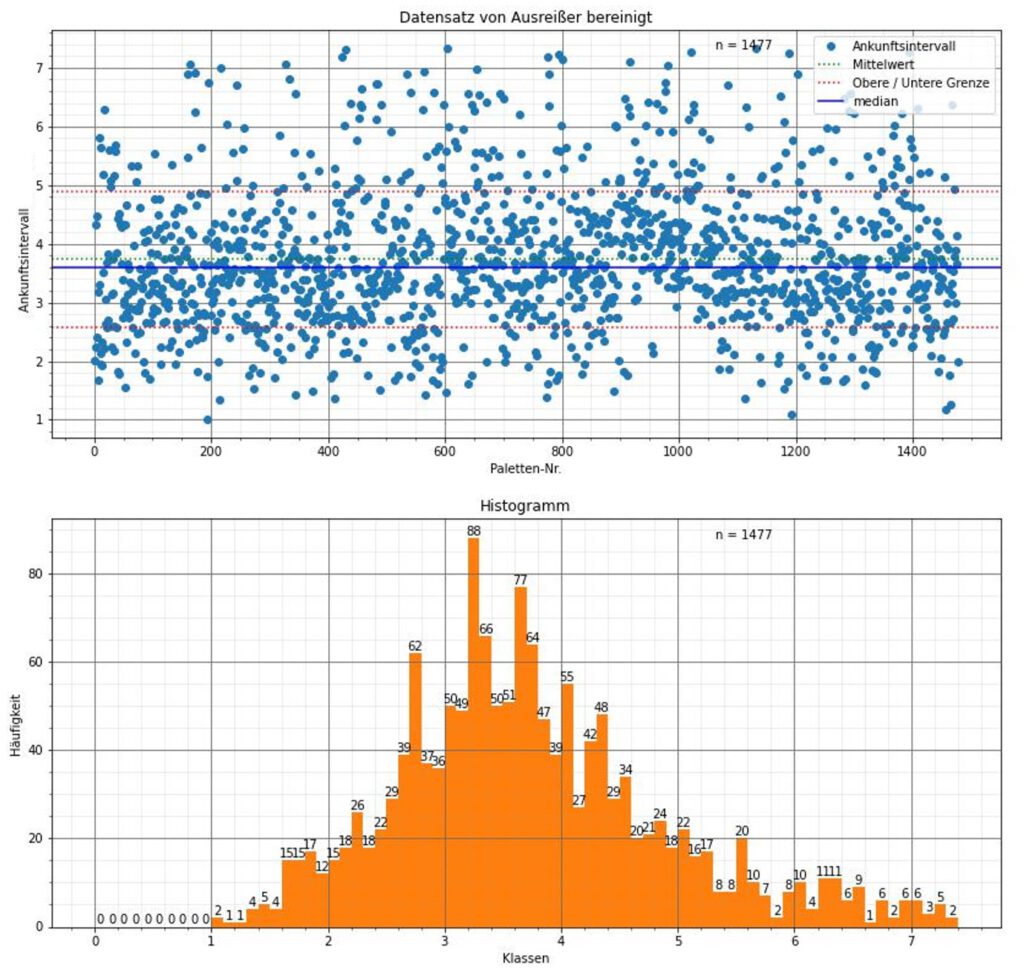
In einigen Fällen, wie beim Aufbau und Betrieb einer neuen Abfülllinie, standen jedoch keine historischen Daten zur Verfügung. In solchen Fällen wurden Erfahrungswerte verwendet, und die artikelspezifischen Verteilungen von bestehenden Anlagen auf die neue Anlage interpoliert.
Die gesammelten und abgestimmten Informationen und Daten wurden in ein entsprechendes, parametrierbares Simulationsmodell überführt, mit welchem die unterschiedlichen Fragen mithilfe von Simulationsexperimenten analysiert und optimiert werden konnten. Hierzu gehört ebenfalls ein entsprechendes Parameterinterface für eine schnelle Parametrisierung des Simulationsmodells sowie ein umfangreiches KPI-Dashboard mit einer Vielzahl an relevanten Kenngrößen.
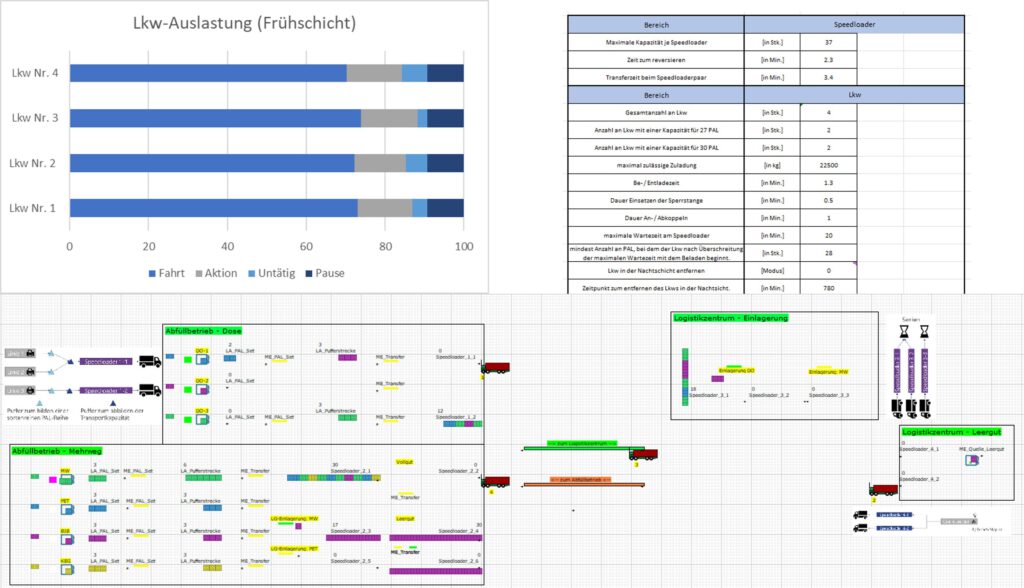
Die durchgeführte Simulationsstudie ermöglichte es, wichtige Erkenntnisse über das Verhalten des Transportsystems zu gewinnen.
Dabei konnte u. a. die Anzahl der erforderlichen Lkw in Abhängigkeit unterschiedlicher Einflussfaktoren dargestellt werden. Beispielsweise kann je nach Schicht oder Wochentag auf den Betrieb eines Lkws verzichtet werden. Zusätzlich ist die Anzahl der Lkw von der Kombination des Produktionsplans abhängig. So konnte aufgezeigt werden, dass bei unterschiedlichen Produktionsplänen, Rüst- und Reinigungszeiten auf den Betrieb von bis zu zwei Lkws verzichtet werden kann. Dies ermöglicht eine flexible Einsatzplanung der Lkw.
Weitere wichtige Erkenntnis aus den Simulationsexperimenten führten zu einer Anpassung des Transportkonzeptes, wodurch weitere Investition in zusätzliches Equipment vermieden werden konnte. Maßgebend dabei war die Frage nach einer sequenziellen oder parallelen Befüllung der automatischen Verladesysteme im Abfüllbetrieb. Hier konnte aufgezeigt werden, dass eine sequenzielle Befüllung der jeweiligen Verladesysteme zu weniger Wartezeiten der Lkw führt im Vergleich zu einer parallelen Befüllung, bei der jeder Abfülllinie einer spezifischen Verladerampe zugeordnet wurde.
Durch die Anpassungen des Transportkonzeptes, basierend auf den Erkenntnissen aus der Simulationsstudie, wurden die Anzahl der automatischen Verladesystem und der Lkw-Auflieger festgelegt. So konnte das Risiko eines Produktionsstopps auf ein wirtschaftliches Minimum reduziert werden, bei gleichzeitiger hoher Auslastung der entsprechenden Lkw.
Wollen Sie Ihre Produktions- und Logistiksysteme digital abbilden und optimieren oder Ihre Ideen und Konzepte durch eine Simulation überprüfen und absichern, dann kontaktieren Sie uns gerne.
Quellen
[1] | Gleitende Mittelfristprognose für den Güter- und Personenverkehr – Mittelfristprognose Sommer 2022. Bonn, Bundesministerium für Digitales und Verkehr, 2022 |
[2] | Günthner, W.; Freudl, G.: Grenzwertbetrachtung, Alternativen zur Staplerverladung – wann ist eine Automatisierung sinnvoll? Lehrstuhl für Fördertechnik Materialfluss Logistik, Technische Universität München, 1999 |
[3] | Meyer, C.; Wiedenmann, R.; Unruh, V.: Automatisiertes Verladen und Ladungssicherung an der Rampe. Online, MMLogsitik, am 19.01.2023 (https://www.mm-logistik.vogel.de/automatisiertes-verladen-und-ladungssicherung-an-der-rampe-a-197322/), veröffentlicht am 06.02.2008. |
[4] | Penno, E.; Weise, S.; Golder, M.: Flexibles LKW-Schnellladesystem. Logistics Journal : Proceedings, Vol. 2020, 2020. |
[5] | Hofstadler, C.; Motzko, C.: Agile Digitalisierung im Baubetrieb – Grundlagen, Innovationen, Disruptionen und Best Practices. Wiesbaden, Springer-Verlag GmbH, 2020 |