Die Planung von verketteten Produktions- und Montageanlagen wird mit zunehmender Anzahl an Produktvarianten und steigenden Flexibilitätsanforderungen stets komplexer [1]. Daher wurden personalintensive Montagetätigkeiten mit vielen Produktvarianten in der Vergangenheit oftmals in Niedriglohnländer ausgelagert. Die steigenden Lohnkosten in diesen Ländern, die zunehmenden Transportkosten als auch die Resilienz-Anforderungen an die Supply Chain führen jedoch zu einem Umdenken [2]. So auch in diesem Fall: Neuplanung einer vollautomatischen Montageanlage für variantenreiche und komplexe Baugruppen, um zwanzig manuelle Montagestationen im Mehrschichtbetrieb durch eine Automatisierung zu ersetzen.
Die Betriebsingenieure (Industrial Engineering) des Produktionsunternehmens können auf langjährige Erfahrungen bei der Planung, Realisierung und den Betrieb von Produktions- und Montageanlagen zurückgreifen. Daher war es möglich mit bekannten und bewährten Anlagenbaugruppen ein Konzept zu entwickeln, dass die technische Umsetzung der vollautomatischen Montage gewährleistet. Um jedoch die damit verbundene hohe Investition wirtschaftlich zu rechtfertigen, bedarf es der Überprüfung und Absicherung der Produktivität/ der Overall Equipment Effectiveness (OEE) der geplanten Anlage, inkl. Bedienkonzept. Hierzu wurde die Durchführung einer Simulationsstudie beauftrage, die das Ziel hatte, das technische Anlagenkonzept zu überprüfen, zu optimieren und die produktspezifischen OEE-Werte für eine Return-on-Investment (ROI) Betrachtung zu ermitteln.
Das technische Konzept der Betriebsingenieure beinhaltete eine Aufteilung der Gesamtanlage in sechs komplexe Montagebereiche, die durch automatisierte Pufferstrecken miteinander gekoppelt sind.
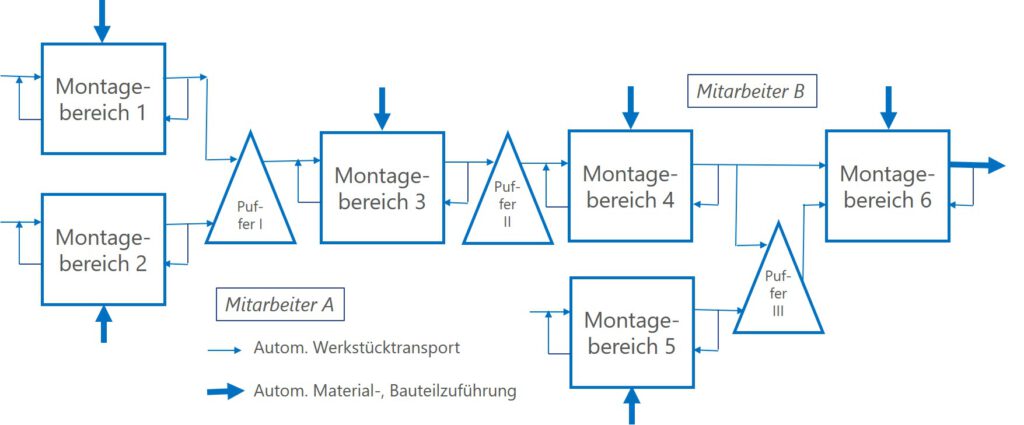
Die kritischen Montagebereiche konnten durch eine wertstromorientierte Zykluszeitanalyse identifiziert werden [3]. Somit war eine vollständige Simulation der sechs Montagebereiche nicht notwendig. In einer ersten Simulationsstudie wurde der kritischste Montagebereich untersucht. Hierzu wurde dieser Montagebereich, bestehend aus:
- zwölf Montageautomaten inkl. Materialzuführung,
- vollautomatischem Werkstücktransport mit Hilfe von Werkstückträgern,
- unterschiedlichen Pufferstrecken zw. den Montageautomaten,
- unterschiedlichen Arten der technischen Störungen (Einzelstörung, Serienstörung, technischer Ausfall),
- Material- und Prüfergebniseinflüssen (fehlerhafte Bauteile werden nicht weiterbearbeitet)
- sowie Mitarbeitereinfluss und dessen Laufwege,
parametrisiert in einem Simulationsmodell abgebildet.
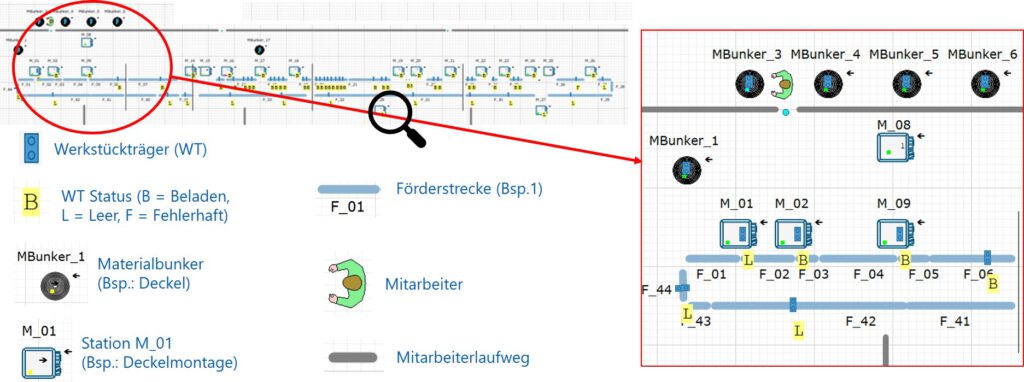
Durch Simulationsexperimente, „Was-Wäre-Wenn-Szenarien“, konnten nicht nur produktspezifische Einflüsse auf den OEE transparent dargestellt werden, sondern auch die jeweiligen Puffergrößen, Transportgeschwindigkeiten und Anzahl an Werkstückträger optimiert werden. Die daraus abgeleiteten Erkenntnisse führten u.a. dazu, dass einzelne Montageautomaten neu dimensioniert wurden. Von großem Vorteil war, dass auf Maschinendaten (MES) von ähnlichen Montagautomaten an anderen Produktionslinien zurückgegriffen werden konnte. Bezüglich der Materialeinflüsse konnten ebenso Daten von ähnlichen Bauteilen herangezogen werden.
Nach Optimierung des kritischen Montagebereiches und Absicherung der produktspezifischen OEEs durch die Simulation, konnte das entwickelte Simulationsmodell ohne großen Aufwand auf die fünf weiteren Montagebereiche übertragen und adaptiert werden. Damit war die Voraussetzung geschaffen die Gesamtanlage in einem Simulationsmodell, bestehend aus den sechs Montagebereichen und den verbindenden Puffer-, Transportstrecken, etc. abzubilden, ohne das fünf zusätzliche Simulationsmodelle entwickelt werden mussten. Auch im Gesamtmodell konnten die Parameter der jeweiligen Simulationsexperimente via Excel-Schnittstelle einfach verändert werden.
Mithilfe der Simulation wurden die Puffer-, Transportstrecken zwischen den Montagebereichen so dimensioniert, dass Einzelstörungen und kurze Bedienereingriffe nicht zu einer Reduzierung der Gesamt-OEE führen. Hierbei konnten auch Produktionsumstellungen, Produktwechsel ohne Rüstprozesse, welche täglich mehrfach notwendig sind, simuliert und deren Einfluss auf den OEE der Gesamtanlage dargestellt werden. Die umfangreichen Rüstprozesse mit Anlagenstillstand werden in den geplanten produktionsfreien Zeitfenstern ausgeführt.
Durch die hier vorgestellte Vorgehensweise konnte zum einen der Simulationsaufwand begrenzt werden, was zu erheblichen Zeit- und Kostenersparnissen führte. Zum anderen konnten durch die Simulation der Gesamtanlage ein Bedienerkonzept, Anzahl Bediener pro Schicht, sowie die produktspezifischen OEE-Werte ermittelt und abgesichert werden. Damit konnte eine ROI-Betrachtung ausgeführt und die Investition positiv entschieden werden.
Wollen Sie Ihre Produktions- und Logistiksysteme digital abbilden und optimieren oder Ihre Ideen und Konzepte durch eine Simulation überprüfen und absichern, dann kontaktieren Sie uns gerne.
Quellen
[1] | Methoden zur Planung modularer, produktflexibler Montagekonfigurationen in der variantenrechen Serienmontage – am Beispiel der Automobilindustrie, Christian Kübler, Dissertation, Fraunhofer-Institut für Produktionstechnik und Automatisierung, IPA, Stuttgart, Fraunhofer Verlage 2017 |
[2] | Kohl, Holger, et al.: White Paper »RESYST« – Resiliente Wertschöpfung in der produzierenden Industrie – innovativ, erfolgreich, krisenfest. Hrsg. Fraunhofer-Gesellschaft e. V., München 2021 |
[3] | Wertstromdesign – Der Weg zur schlanken Fabrik, Klaus Erlach, 3. Auflage, VDI-Buch, Springer Verlag, Berlin, 2020 |